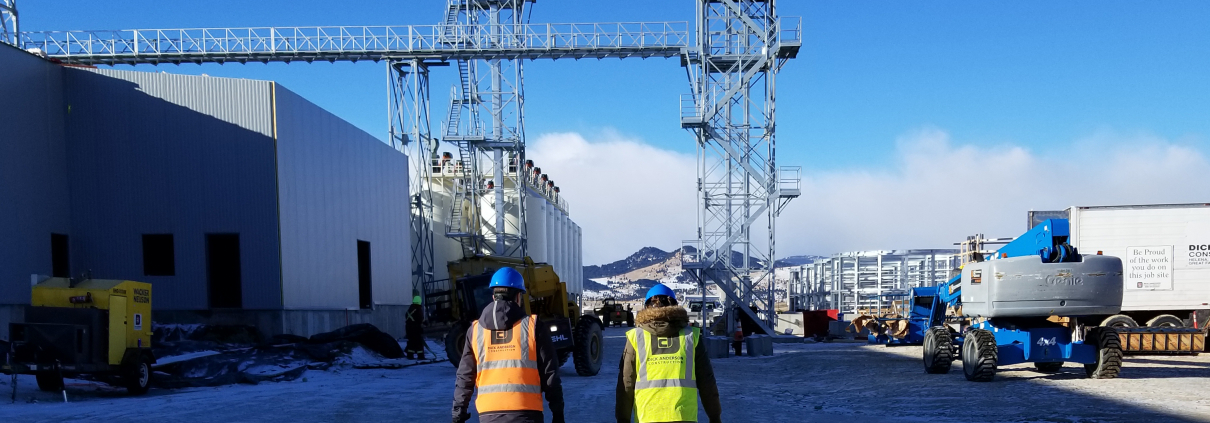
Manufacturing and Industrial Efficiency Toolkit
Manufacturing and industry is the third largest energy-consuming sector in the U.S. economy, behind electric power generation and transportation. This is easy to understand when you consider that this sector is responsible for everything from processing raw materials like natural gas, oil, metals, and agricultural products to manufacturing new products, like homes and cars.
In fact, the majority of energy consumption goes specifically toward process-related activities, whether it’s heating a smelter for purifying metals, or generating heat and pressure conditions for chemical processes, such as those needed for manufacturing products like plastic. These energy-consuming processes typically rely on oil or coal for meeting the high energy demands.
The second most consumptive part of the industry sector is that related to powering auxiliary or “supportive system” equipment such as motors, pumps, fans, and product transporting equipment like conveyor belts and lifts. This equipment relies largely on electricity.
The buildings themselves use a relatively small portion of the industrial sector’s overall energy use. However, this doesn’t mean the potential energy savings should be overlooked. Ensuring that the building’s HVAC system, lighting, and appliances are working as efficiently as possible is essential in lowering energy use. Refer to our specific toolkits to learn more about improving these areas.
Increasing energy efficiency
Because the industrial sector and its processes vary widely, it is nearly impossible to identify improvements that are applicable to every manufacturer. Therefore, the best way to understand how to lower energy costs and increase efficiency is to have an independent audit done. This will allow energy professionals to line out potential energy-saving opportunities specific to the processes and needs of the building. While some of these recommendations may involve replacing or upgrading equipment, many will simply involve implementing better energy-management practices, such as installing a variable speed drive on motors, educating employees on best management practices, and utilizing energy analysis software to detect irregularities that may indicate problem areas.
ENERGY STAR offers several informative and comprehensive guides on specific industrial energy-efficiency improvements, including everything from automotive manufacturing to breakfast cereal production.
Auxiliary Equipment
Pumps, motors, and compressed air systems, while an essential part of any manufacturing plant, can contribute to some of the greatest inefficiencies related to energy use. Below is a list of strategies to consider when looking to increase energy efficiency in these areas.
Pumps
- Understand warning signs of inefficient pumps. This can include excessively noisy operation, high maintenance requirements, and strained control valves.
- Ensure pumping systems are correctly sized for operational needs. This may require replacing the current pump with more appropriately sized equipment. To determine correct pump sizing, refer to this article by Sean Moran.
- If replacing the pump is not feasible, replacing the pump impeller with a more appropriately sized impeller can provide an effective alternative.
- Lastly, adjust the pipe configuration within the pumping system to ensure materials flow efficiently. This includes ensuring proper pipe sizing, reducing or eliminating sharp pipe angles (90⁰ or more), and redesigning the pipe layout to reduce pressure drops.
Motors
- Motors are often sized to meet peak energy demands. While suitable when the system is operating at peak level, this sizing approach can lead to extensive energy waste when a system is operating at lower demand. Designing a specialized system to meet varying operating conditions can help reduce this waste. Generally, it’s best to size motors for about 75% of peak energy demand.
- If replacing a motor is not feasible, adding a variable speed drive on an existing motor can help reduce waste when a system is operating at lower demand. This can also improve system life as it reduces wear and tear, as well as productivity levels as the motor speed is better matched for system processes.
Compressed Air Systems
- Monitor the system for leaks. Leaks can waste 20-30% of a system’s energy output.
- Fix leaks promptly. Leaks most often occur near joints and other connections. Invest in quality fittings and utilize joint sealant to ensure the best possible fit. Ensuring leaks are found and promptly mitigated ensures that the system can maintain appropriate pressure, operating levels, and energy efficiency.
- Lower the air pressure of the system if possible. A lower flow pressure reduces strain on equipment and mitigates potential air leakage rates.
Waste Heat Recovery
According to the U.S. Department of Energy, 20-50% of industrial energy inputs are given off as waste heat. This can come in many forms such as heat radiated from heating equipment, hot exhaust, cooling processes, etc. Capturing this heat and rerouting it back into a system process can be a great way to decrease these energy losses and make an industrial system more efficient.
The capturing method depends greatly on the industrial processes present at a particular site. However, software products are available to educate energy coordinators and plant managers on potential areas of improvement specific to the manufacturing plant. One such program is the Process Heating Assessment Survey Tool (PHAST). This program takes historic energy data supplied by the user, and processes a series of informative guides that educate coordinators on how to run equipment more efficiently.
Energy Production
Some energy costs can be offset through onsite energy production using solar, wind, and other renewable-energy sources. Not only can this reduce energy costs, it can also reduce greenhouse gas emissions (depending on the type of energy used), lead to greater energy resiliency, and be a potential revenue source for industries.
Quick tips for improving energy efficiency
Despite the variation in the industrial sector’s energy consumption needs, there are still general practices that can be implemented in a majority of areas to increase energy efficiency. Below is a list of potential improvements:
- Install VFDs on motors and pumps where possible to control energy use more accurately. This can increase both energy efficiency — up to 60% savings — and production efficiency. See the motor toolkit for more information.
- Upgrade to LED lights. Visit the lighting toolkit for more information.
- Maintain energy-management software and equipment to determine areas of inefficiencies. Educate employees on detecting inefficiencies and how to fix them promptly.
- Ensure that set points on energy-control systems like lighting sensors, thermostats, and automatic shut off systems are adjusted regularly and in functioning order.
- In the case of a boiler system, insulating steam and condensate lines and maintaining steam traps can prevent leakage and can save up to 20% of an industrial plant’s energy use.